Costing cents to produce and often given away as part of promotions, the natural inclination of distributors and clients alike is to find the most affordable buttons possible. The thought being, a button is a button. The reality is, a few cents in savings often leads to a drastic reduction in quality. Custom made buttons can be produced in a variety of ways. Two of the most common are one piece and two piece construction.
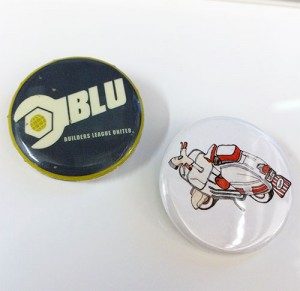
At first glance, these buttons may appear similar. They are round, 1.5″ in diameter and have a safety pin back. The button on the left is a one piece button. The button on a right is a two piece button. So what’s the difference? Look closely. The button on the right has a smooth rim (edge). The button on the left, not so much. It may be hard to tell from the picture, but the rim of the button on the right is ragged. The raggedness is a direct result of the manufacturing process.
One piece buttons are produced by taking a laminated graphic and crimping it into a metal pinned back. Two piece buttons can be laminated or produced with a mylar covering (we will make a post in the future about the pros and cons of both options). The graphic is then placed on a metal shell. The protected graphic and shell are then crimped together.
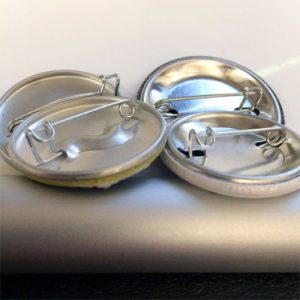
Take a look at the backs of both the buttons. Here you can really start to see how these products differ. Again the button on the left is a once piece button and the button on a right is a two piece button. See that ridge on the one piece button? That’s a defect. During the crimping process, the plastic laminate was pushed up by the metal back, exposing the paper graphic. Now, look at the button on the right. The graphic and mylar (protective plastic covering) have been crimped over then under the edge of the shell, sealing out the elements. This process creates a rim (edge), which additional information like phone numbers and web addresses can be printed.
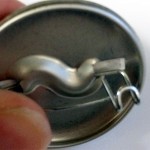
The key difference between a one piece and a two piece button is the shell of a two piece button. The shell supports and protects the graphic. Without a shell, the graphic of a one piece button is exposed on the back, as seen in the image to the left. This is a major vulnerability. Not only can moisture attack and ruin this button, but apply a little pressure on the pin from the back and you can push the pin up and into the face of the button causing a permanent defect. It doesn’t take a lot of pressure, and it often happens during shipping. Push a little harder, you can poke right through!
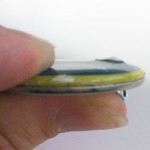
Not only does the shell protect two-piece buttons from the elements as well as the pin, it holds the pin in place, eliminating rattling. The pin in a one piece button can slide back and forth as well as up and down. When worn, a one piece button will rattle.
Why would anyone choose a one piece button over a two piece? Cost. They have fewer parts, so they cost less to produce and ship. However, the overall quality suffers. If buttons are how you will be introducing your brand to someone, what sort of impression do you want to make?